We use cookies to make your experience better. To comply with the new e-Privacy directive, we need to ask for your consent to set the cookies. Learn more.
The complexity of 3D printed part shapes
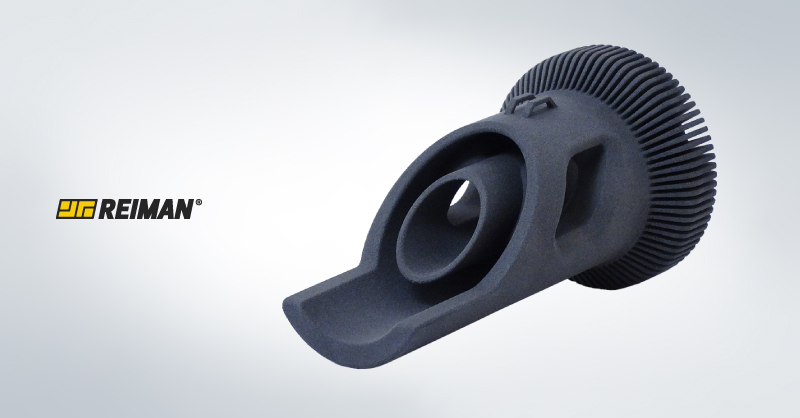
It is important that a 3D printed part serves its purpose in its entirety, and it is often necessary for its design to be complex to achieve the most necessary and crucial goals. For the final piece to demonstrate exactly the complex shape previously thought out and designed, the following steps are required:
Technology and Material Selection
To ensure that the complex design of the part meets all the criteria, the process must begin by selecting the right material for the intended application. Depending on the material selected, it will also be known which technology will be used to produce the part, as each additive manufacturing material is associated with a technology.
Once the material and technology have been selected, the design is developed according to the features and skills of the selected technology. Depending on the details the part needs to have, each technology is classified with different specialized features.
Design Optimization
It is important that all the details applied to the design of the part can be reproduced with good results, so that the entire result is presented correctly. Significantly thin or small attributes may not be printed correctly, due to the machine not being able to reproduce them and are also prone to breaking during application. The purpose of an optimized design is not only to ensure successful printing, but also to ensure that the printed part is resistant and durable in all its aspects.
Support Structures
Details such as overhangs or arches are shapes that extend beyond the previous layer or that cross a space without any support. In this case, support structures are added to the part design so that the part is produced, guaranteeing the final design after printing, and preventing overhangs or arches from collapsing or deforming during printing. However, it is important to understand the necessary quantity and location of structures to be implemented in the design, so that it is easy (and/or possible) to remove them from the part, without spoiling the final shape, and without wasting too much material.
This stage of production is best suited to parts produced in FDM and SLA technologies. In the case of SLS, the polymer powder block replaces the purpose of the support structures because the final SLS part will be developed inside the block.
Definition Adjustments
As each material produces a different output effect, it is important that the printer has its settings adjusted to the material used for printing. Some of the settings available for adjustment are layer thickness, infill, speed, temperature, and cooling. With different setting adjustments, it is possible to achieve a more refined result that each material can provide during production.
Printing Process
At this stage, the printer follows the design path to build the part, layer by layer. With all the details of the complex design well structured, and with the settings well-adjusted according to the material used, the printer can capture all the design information to obtain a solution that is rigorously close to the planned design.
Post-Printing Treatment
After the printer has finished printing, the part can be refined with different finishing methods, depending on the printed material. From removing support structures on an SLA part, surface polishing on an SLS part, or spray painting on an FDM part, the ideal treatment for the complex part turns it into a more professional and resistant part.
Get to know about RMN Additiveadditive manufacturing solutions. If you need a suitable solution for your project, contact us by phone or on our website at www.reiman.pt