We use cookies to make your experience better. To comply with the new e-Privacy directive, we need to ask for your consent to set the cookies. Learn more.
Modernizing Maintenance: Integrating Technology with PTC Thermistors
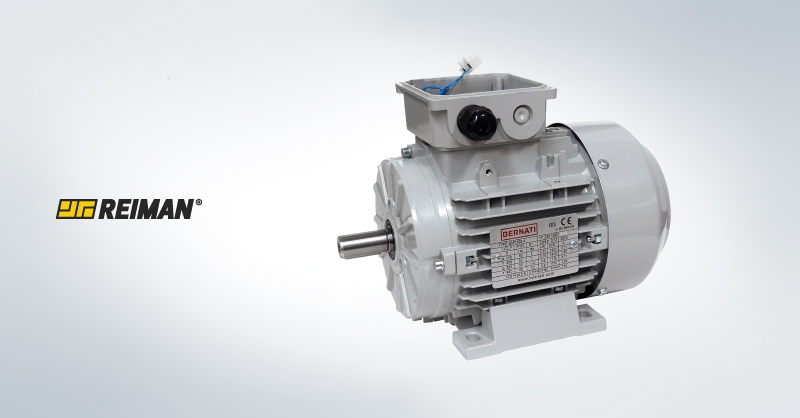
In the era of Industry 4.0, maintenance is increasingly evolving beyond simply fixing problems. Technology now plays a crucial role, and PTC (Positive Temperature Coefficient) thermistors are emerging as a smart solution.
These small yet powerful thermistors monitor the temperature of electric motors in real-time. When they detect anomalies such as overload or overheating, they act swiftly by interrupting the motor's operation to prevent serious damage.
By integrating PTC thermistors into electric motors, for instance, companies ensure safer operation, reduce downtime, and prolong equipment lifespan. It's a paradigm shift that places technology not just as a supplement but as the focal point of modern maintenance.
How do these thermistors fit into the broader landscape of motor monitoring systems?
Motor control and monitoring systems, increasingly sophisticated, are designed to track motor performance in real-time. They gather vital data such as temperature, vibration, and current, analysing them to detect patterns and trends that may indicate impending issues. This is where PTC thermistors come into play.
PTC thermistors, with their ability to monitor motor temperature, provide a crucial data point for these monitoring systems. They offer real-time information about the motor's thermal condition, enabling a rapid response to any signs of overheating. PTC thermistors are highly reliable and durable, making them an ideal choice for demanding industrial environments.
By integrating PTC thermistors into motor monitoring systems, companies can create a comprehensive approach to predictive maintenance. Instead of waiting for a potentially disastrous failure, operators can anticipate issues and take proactive measures to prevent them. This not only reduces costs associated with corrective maintenance but also enhances operational efficiency and equipment availability.
Moreover, integrating PTC thermistors into motor monitoring systems enables a deeper analysis of collected data. By correlating PTC thermistor readings with other variables such as vibration and current, operators can identify complex patterns and gain a better understanding of motor behavior under various operating conditions. This can lead to more precise and detailed adjustments in processes, promoting improvements in energy efficiency.
However, to make the most of the potential of PTC thermistors and engine monitoring systems, it is essential to invest in proper training for operators. It is important to understand how to interpret the data generated by the systems and take appropriate actions. It is also important to know that regular maintenance of the PTC thermistors themselves is fundamental to ensuring their reliability in the long term.
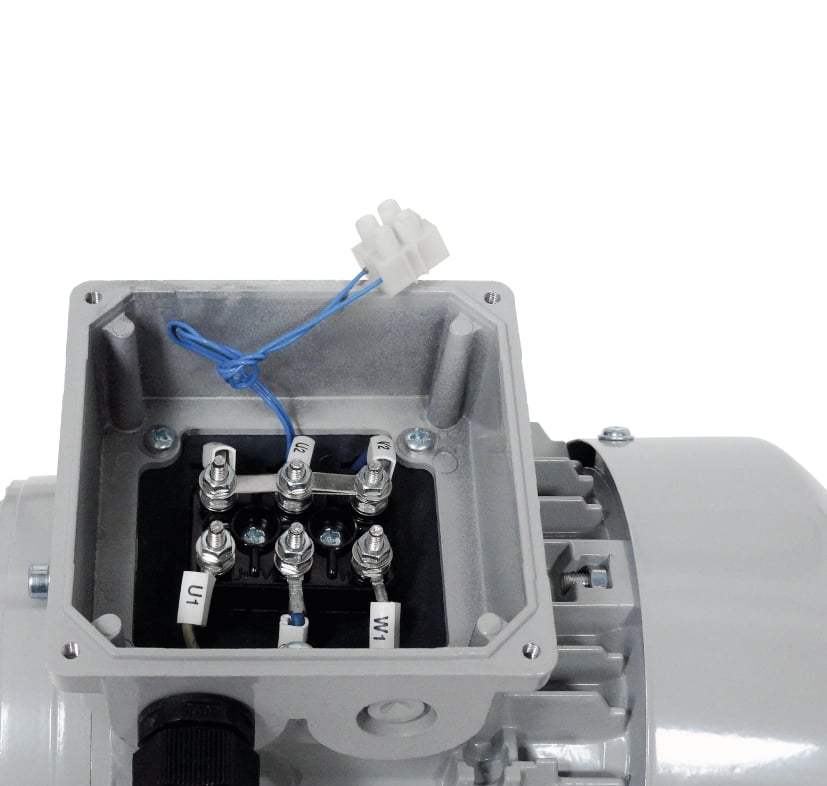
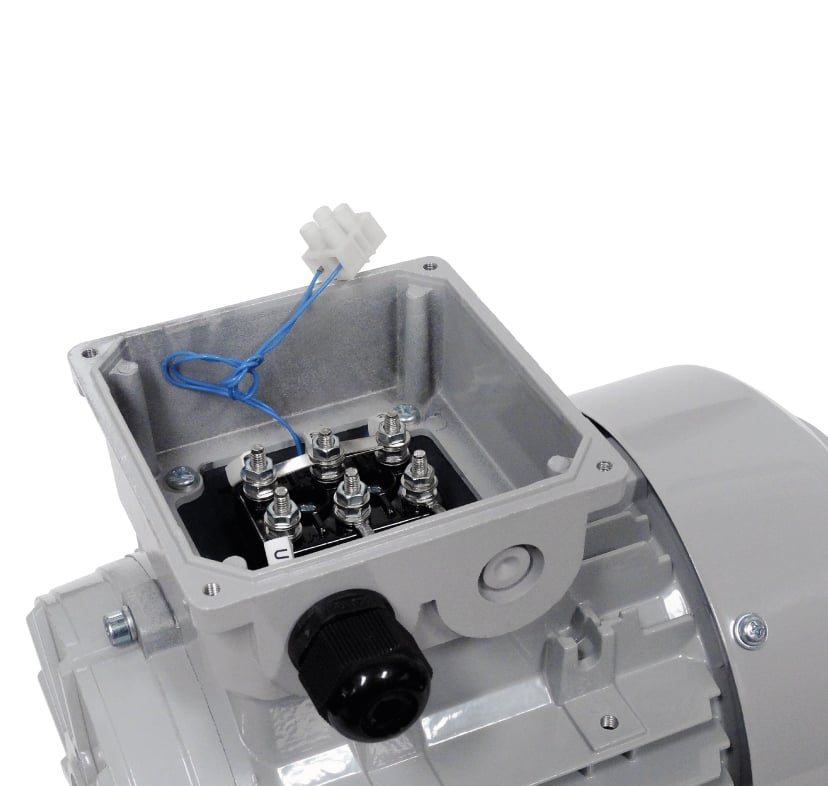
Motor control and monitoring systems, increasingly sophisticated, are designed to track motor performance in real-time. They gather vital data such as temperature, vibration, and current, analysing them to detect patterns and trends that may indicate impending issues. This is where PTC thermistors come into play.
PTC thermistors, with their ability to monitor motor temperature, provide a crucial data point for these monitoring systems. They offer real-time information about the motor's thermal condition, enabling a rapid response to any signs of overheating. PTC thermistors are highly reliable and durable, making them an ideal choice for demanding industrial environments.
By integrating PTC thermistors into motor monitoring systems, companies can create a comprehensive approach to predictive maintenance. Instead of waiting for a potentially disastrous failure, operators can anticipate issues and take proactive measures to prevent them. This not only reduces costs associated with corrective maintenance but also enhances operational efficiency and equipment availability.
Moreover, integrating PTC thermistors into motor monitoring systems enables a deeper analysis of collected data. By correlating PTC thermistor readings with other variables such as vibration and current, operators can identify complex patterns and gain a better understanding of motor behavior under various operating conditions. This can lead to more precise and detailed adjustments in processes, promoting improvements in energy efficiency.
However, to make the most of the potential of PTC thermistors and engine monitoring systems, it is essential to invest in proper training for operators. It is important to understand how to interpret the data generated by the systems and take appropriate actions. It is also important to know that regular maintenance of the PTC thermistors themselves is fundamental to ensuring their reliability in the long term.
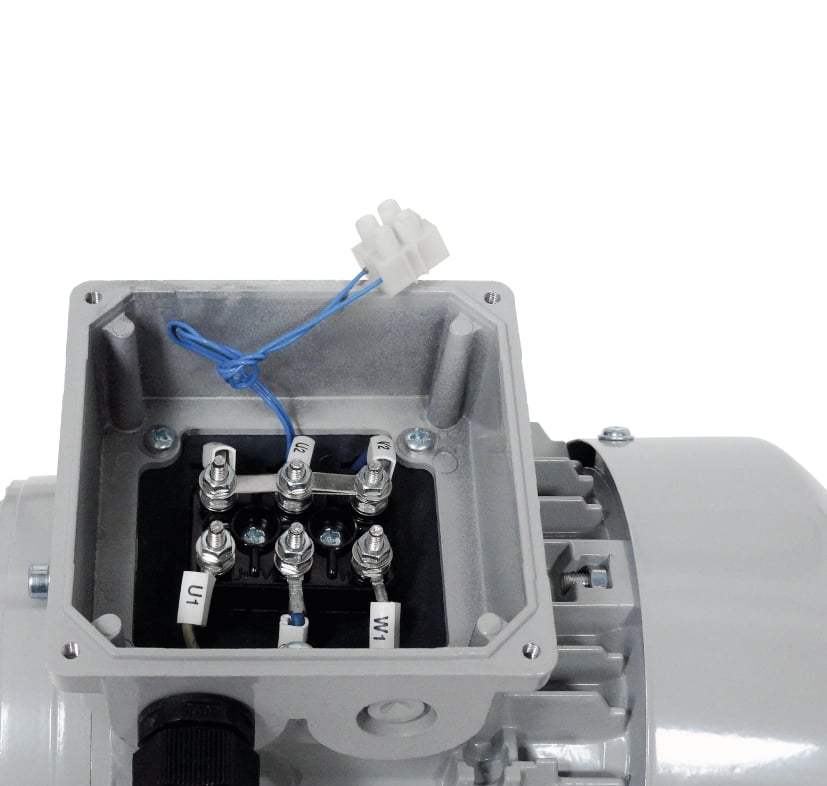
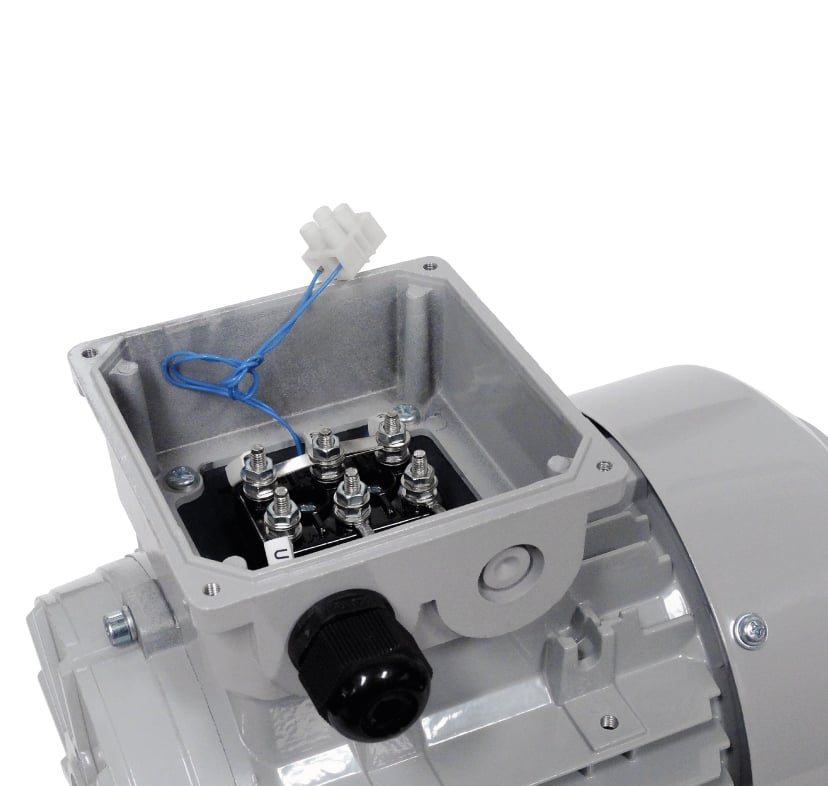
Motor control and monitoring systems, increasingly sophisticated, are designed to track motor performance in real-time. They gather vital data such as temperature, vibration, and current, analysing them to detect patterns and trends that may indicate impending issues. This is where PTC thermistors come into play.
PTC thermistors, with their ability to monitor motor temperature, provide a crucial data point for these monitoring systems. They offer real-time information about the motor's thermal condition, enabling a rapid response to any signs of overheating. PTC thermistors are highly reliable and durable, making them an ideal choice for demanding industrial environments.
By integrating PTC thermistors into motor monitoring systems, companies can create a comprehensive approach to predictive maintenance. Instead of waiting for a potentially disastrous failure, operators can anticipate issues and take proactive measures to prevent them. This not only reduces costs associated with corrective maintenance but also enhances operational efficiency and equipment availability.
Moreover, integrating PTC thermistors into motor monitoring systems enables a deeper analysis of collected data. By correlating PTC thermistor readings with other variables such as vibration and current, operators can identify complex patterns and gain a better understanding of motor behavior under various operating conditions. This can lead to more precise and detailed adjustments in processes, promoting improvements in energy efficiency.
However, to make the most of the potential of PTC thermistors and engine monitoring systems, it is essential to invest in proper training for operators. It is important to understand how to interpret the data generated by the systems and take appropriate actions. It is also important to know that regular maintenance of the PTC thermistors themselves is fundamental to ensuring their reliability in the long term.
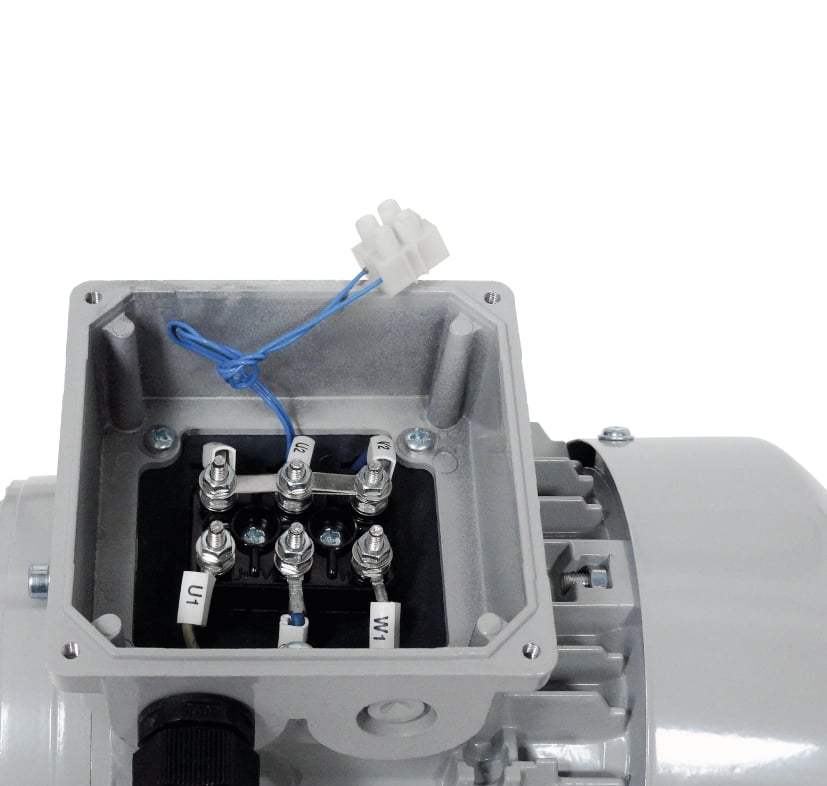
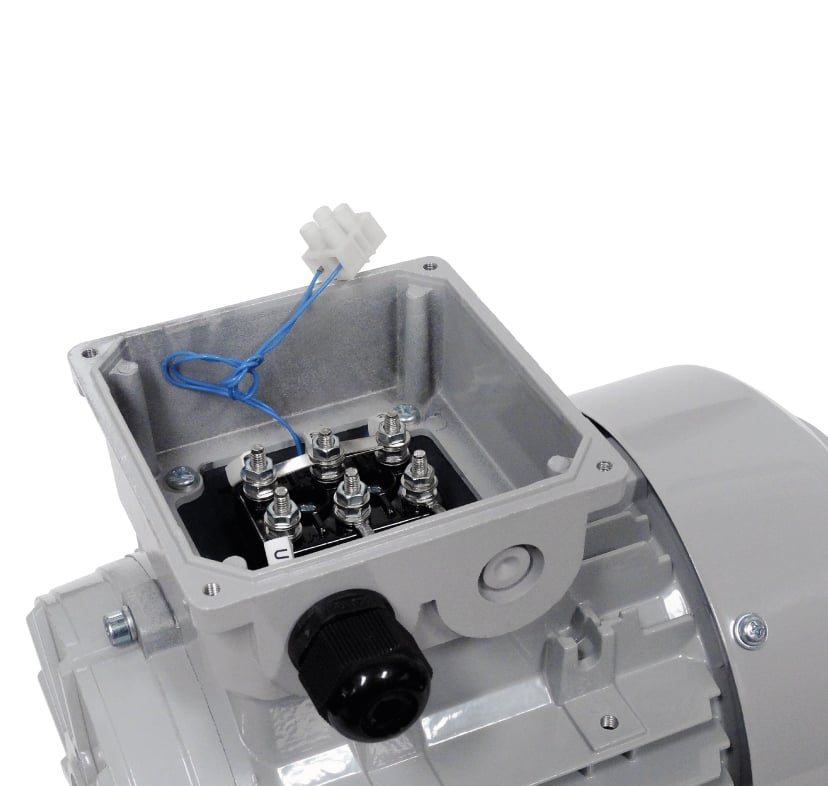
In summary, PTC thermistors represent a crucial piece in the puzzle of modern maintenance.
By integrating them into other monitoring and control systems, the approach to maintenance shifts from a reactive mindset to a proactive and predictive one, increasing not only the reliability and efficiency of equipment but also driving competitiveness in the market.
Discover the high-energy efficiency electric motor solutions and accessories offered by REIMAN.