We use cookies to make your experience better. To comply with the new e-Privacy directive, we need to ask for your consent to set the cookies. Learn more.
What is SLS? (Selective Laser Sintering)
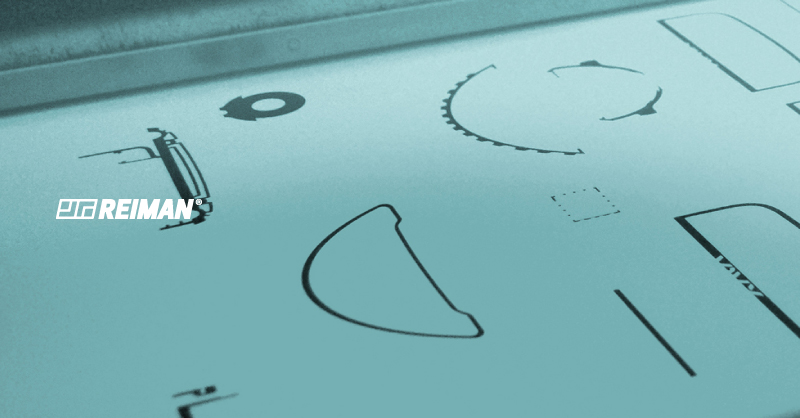
RMN Additive presents a new technology in their 3D printing function panel, which production method sums it up to a sintering process on a polymeric powder through a laser beam, layer by layer. SLS technology (Selective Laser Sintering), primordially developed in the mid 1980’s, and recently innovated for more effective and sustainable needs, is the most preferred technology by industry professionals, due to its productivity and capacity in printing practical and resistant parts.
How Does SLS 3D Printing Work?
A thin layer of dust polymer is spread all across the platform where the printed part will be produced. This platform is implemented on the build chamber with controlled temperature and humidity, in order to assure that the laser, in charge of sintering each part's layer, has the ideal conditions to execute. After the sintering process of a certain layer, a platform lowers slightly a bit, and a new amount of polymer is transferred from the powder delivery system to the build chamber, exacly above the previously sintered layer. In this stage, the laser immediatly sinterizes the following layer and, subsquently, the printed part starts getting built. The unsintered layer is kept in the same space, serving itself as a support for structures that will appear in superior layers. After the printing is finished, the build chamber must be slowly cooled down so that it can be possible to extract the printed part from the build chamber and, with that, remove the unsintered dust. This dust is picked up so that it can be reused in the next printing session.
Which Material is Used for SLS Production?
The most used material for SLS 3D printing production is Nylon (PA or Polyamide), a thermoplastic which is strong, long-lasting and resistant to water, light and different degrees of temperature. According to the molecular structure of this polymer, Nylon can gather multiple names, usually characterized by numbers, for example, PA12. These different molecular structures allow the existence of various types of polyamides with different carachteristics between themselves and, therefore, applications. The models that RMN Additive appropriate for production are as follows:
EON PA12 – A polymer dust, based on polyamide 12, versatile for multiple applications.
Material Properties:
- High Tensile Strength
- Ductility
- Environmental Stability
- High Temperature Resistance
- Durable
- Minimal Water Absorption
Common Applications:
- High Performance Prototyping
- Fixtures and Tooling
- Permanent Jigs
- End-Use Parts
- High Performance Prototyping
EON PA12-GF – A glass-filled polymer with a higher capacity inthermal and chemical resistance, in comparison to EON PA12.
Material Properties:
- High Rigidity
- Dimensional Accuracy
- Thermal Stability
- High Temperature Resistance
- Durable
- Environmental Stability
Common Applications:
- Fixture Undergoing Long-Term Sustained Loading
- Stiff Structural Components
- End-Use Industrial Parts
- Thermally Stressed Housings
- Fixture Undergoing Long-Term Sustained Loading
What Are the Advantages of Choosing SLS Technology for the Production of 3D Parts?
Practical Design
While certain areas from each layer are solidified, the remaining unsintered dust serves as a support structure for other SLS printed part productions, which makes it possible for more freedom of the printed part’s design. Therefore, geometry features which are more complex and unviable in other technologies are possible thanks to this detail this technology has in its advantage.
Sustainability
Such as in terms of high amounts in one production, as well as recycled material management, this technology matches a satisfying level of saving time and resources. An SLS 3D printing production, apart from usually being faster than FDM and SLA, can also gather a big quantity of parts in one printing cycle. Be it a one-unit reproduction, or more units, the printing cycle matches the same period of time if the increase in printed units does not correspond necessarily to the increase of the printed cake's size.
Correlation Between Technology and Material
Nylon provides versatility in characterizing properties in printed parts, so much in prototypes as well as in end-use parts. SLS method production attributes total density to the printed part apart from assuring an excellent dimensional accuracy and control. All of this highlights a great technology-material ratio where it is possible to obtain products for different finishings (depending on the chosen material) through a process in which this technology itself has obtained characteristics no other technology has.