We use cookies to make your experience better. To comply with the new e-Privacy directive, we need to ask for your consent to set the cookies. Learn more.
Restart Prevention for Press Machinery
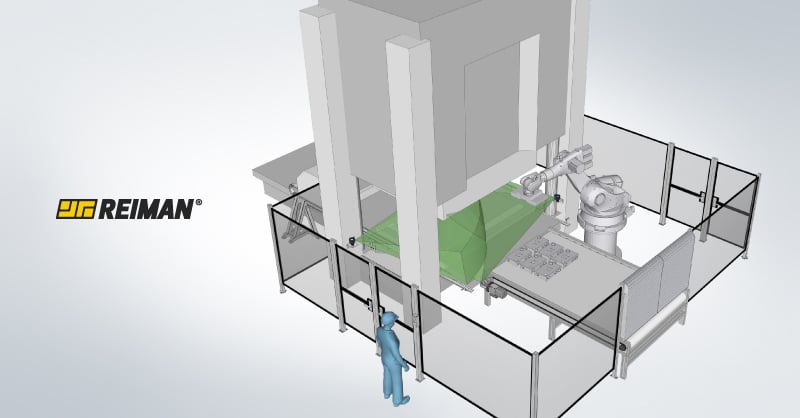
Industrial presses are a traditional equipment that requires a very high level of security due to the potential severity of possible damage.
However, because of technological limitations, to this day, the combinations of devices that are normally incorporated cannot guarantee 100% safety for the operator exposed to the risks.
In addition, some of the built-in devices require human intervention, sometimes a long one, such as Lockout-Tagout, lowering the production of the equipment.
In this way, productivity and volume of waste are often negatively influenced by these safety devices. Mainly due to the occurrence of false positives, caused by the existence of debris or process conditions, such as oil splatters and dust.
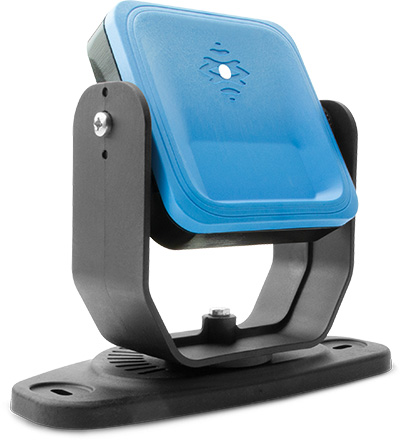
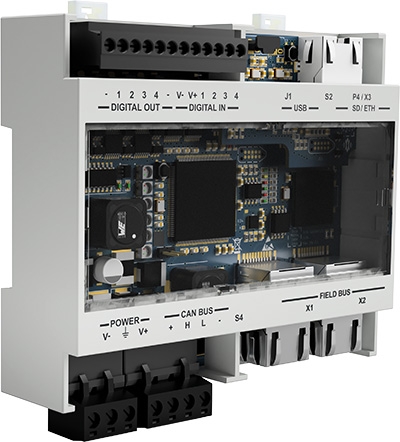
A new approach to machine safety is the use of Inxpect’s safety radar technology, certified for industrial use, performing volumetric control and motion detection combined with process noise immunity, in an open field.
Inxpect's radar technology has two modes of operation:
- Access Protection: Ensures that the operator is always detected before reaching the danger zone.
- Restart Prevention: Ensures that when the operator is in the danger zone, the subject is always detected.
They can be used in a dedicated or combined way, depending on the analysis.
Depending on the configurations, Inxpect sensors can detect micro-movements of the human body, including a person's breathing and heartbeat, and be highly robust against surrounding conditions such as smoke, dust, debris and light sources.
These features allow Inxpect sensors to be reliable even in the harshest conditions, allowing a significant reduction of risk exposure.
After risk analysis validation, the possibility of using the automatic restart prevention function allows the undeniable increase of the equipment availability for work and tasks flexibility, ensuring the safety of persons and goods.
Inxpect guarantees the highest safety solution with the 200 series sensors!
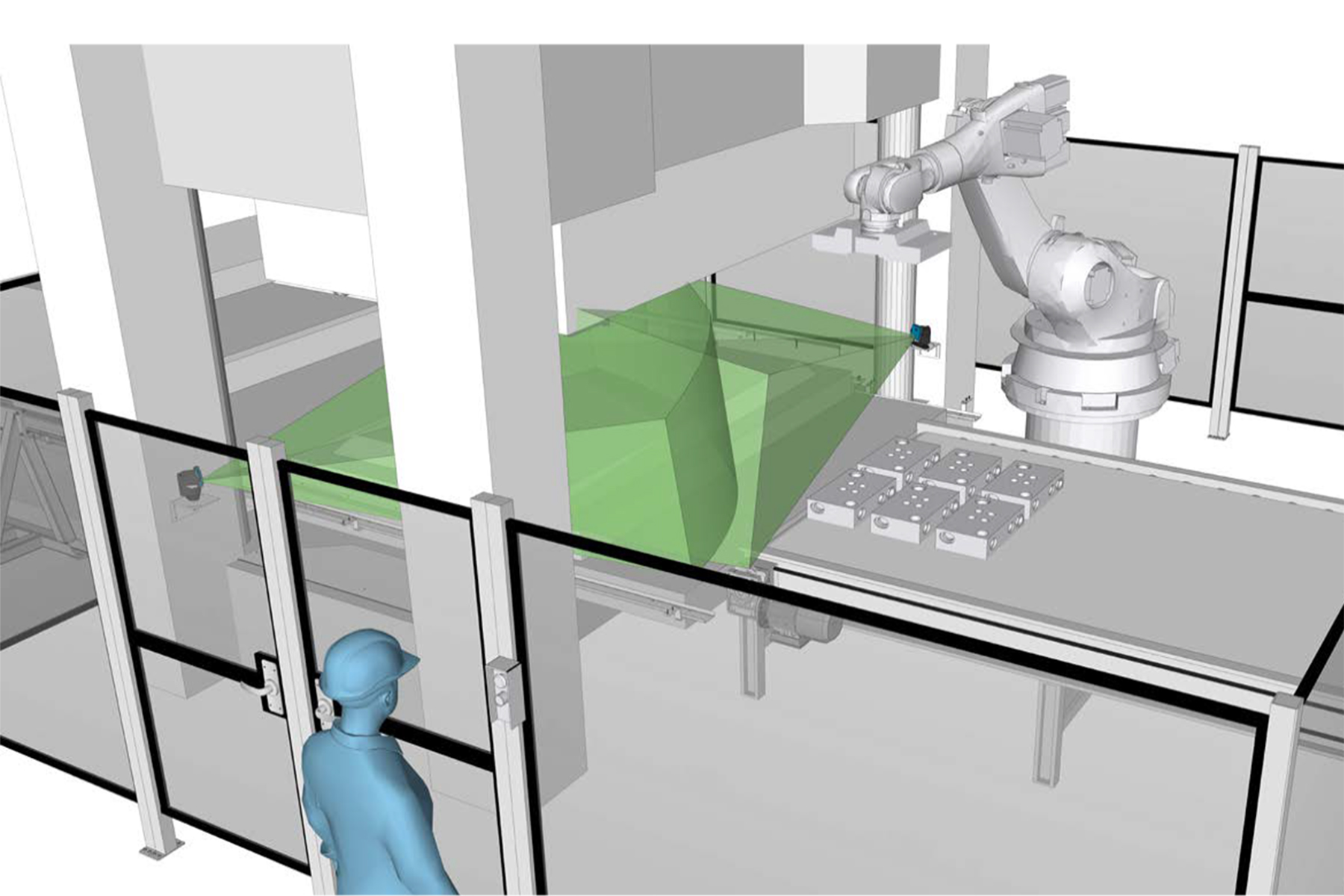
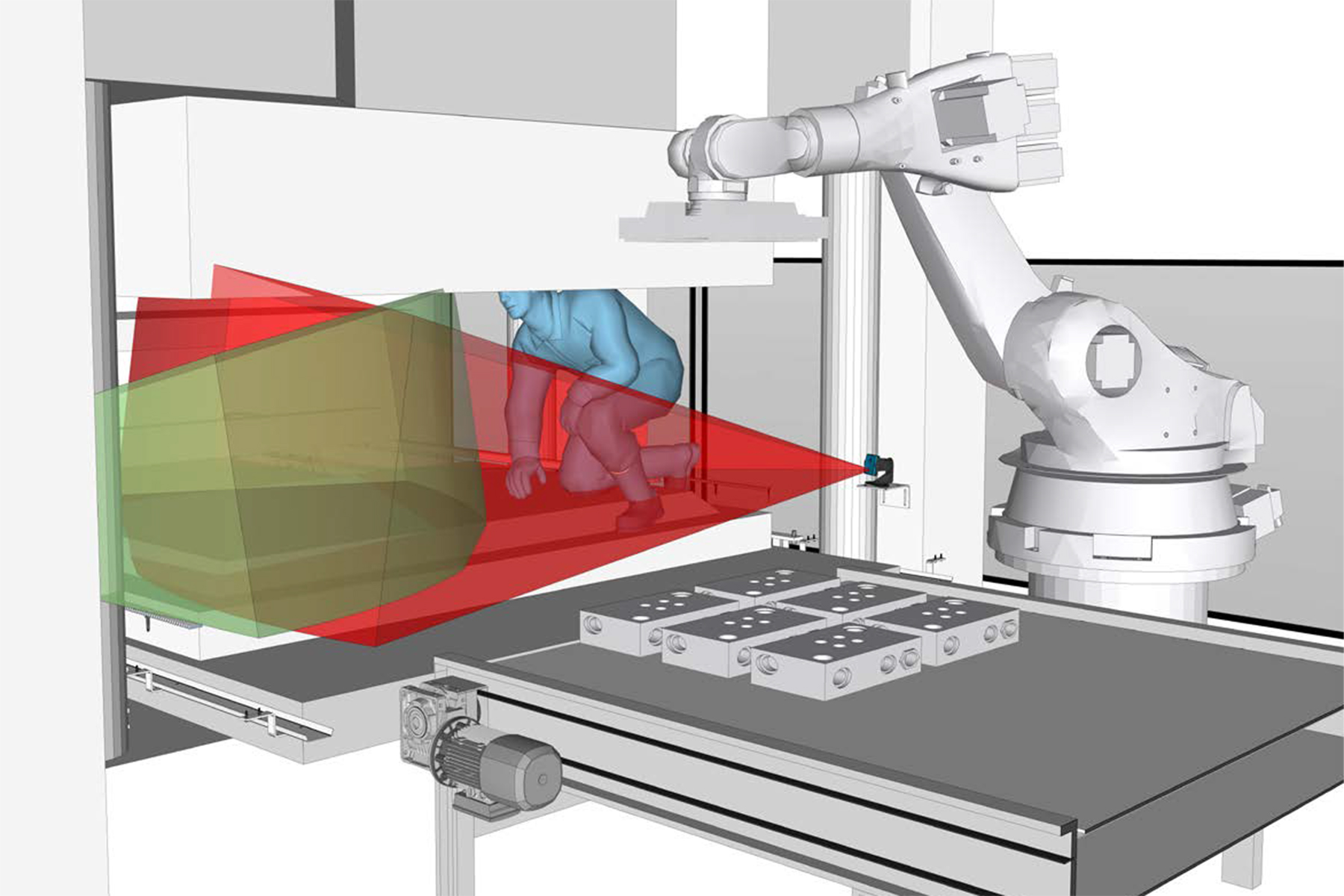
A possible configuration of the Inxpect system on a press machine is by using two 200 series sensors, placed at opposite vertices of the risk volume, and each one of the volumetric control prisms properly configured to ensure detections throughout the volume to be controlled.
This will guarantee that there are no humans inside the volume immediately before the press performs its main task, ensuring a safety restart of the machine, even in extreme conditions.
Inxpect sensors are compliant with ISO 16092, the safety standard for mechanical presses.
The standard ISO 16092-1 states that “when people can remain in the hazardous zone(s) without being visible to the operator, a means to prevent restart shall be provided, for example, a presence-sensing device or door closure inhibition by captive keys. The means shall conform to the required performance level given in PL tables in the relevant parts of the ISO 16092 series."nas tabelas PL das partes pertinentes da série ISO 16092.”
With this, Inxpect sensors are qualified to work in press machines environments, simplifying the interaction between operator and machines.
In addition to solving industrial safety issues, Inxpect’s radar technology brings several advantages:
- Reduce restart time and increase productivity.
- Increase safe operation press. If an operator is still in the area when the machinery tries to restart, Inxpect Smart Sensors will recognize the subject and prevent machinery from restarting.
- Cost efficient: one control unit can be linked up to six smart sensors.
- Complies with standard:
UNE-EN ISO 16092-1, UNE-EN ISO 16092-2;
UNE-EN ISO 16092-3, UNE-EN ISO 16092-4;
(PLd required by the standard).