We use cookies to make your experience better. To comply with the new e-Privacy directive, we need to ask for your consent to set the cookies. Learn more.
3D Printing in Polymers: A Guide to Selecting the Ideal Process
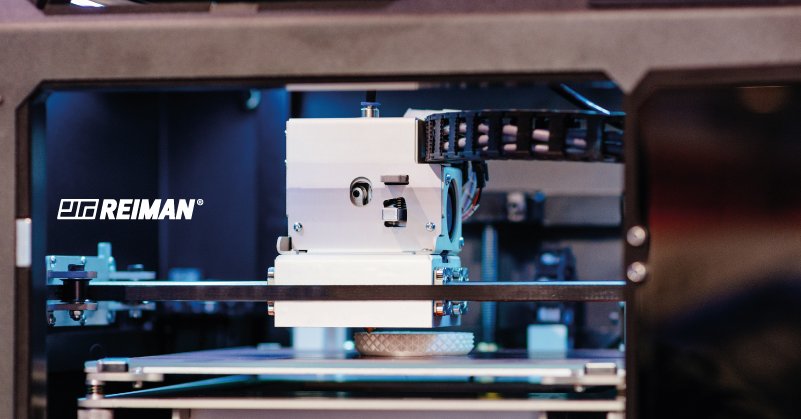
3D printing, or additive manufacturing, in polymers offers a world of possibilities for creating prototypes, complex parts, and customised products. However, the variety of available technologies and materials can make it challenging to choose the ideal process for each challenge. In this guide, REIMAN, in collaboration with RMN Additive, presents the key criteria for a more informed selection.
1. Selection of the Process Based on Material
Thechoiceofpolymeris crucial to ensuringthedesiredproperties. Both thermoplasticsandresinsneed to beconsidered. For thermoplasticparts, manufacturingiscarried out using FDM (FusedDepositionModeling) and SLS (Selective Laser Sintering) technologies.
The FDM (Fused Deposition Modeling) process offers an economical and versatile production of a wide variety of geometries, making it ideal for rapid prototyping and parts with moderate mechanical requirements.
SLS (Selective Laser Sintering) enables the production of parts suitable for high-performance industrial applications, with greater durability and a higher level of complexity, without the need for support structures.
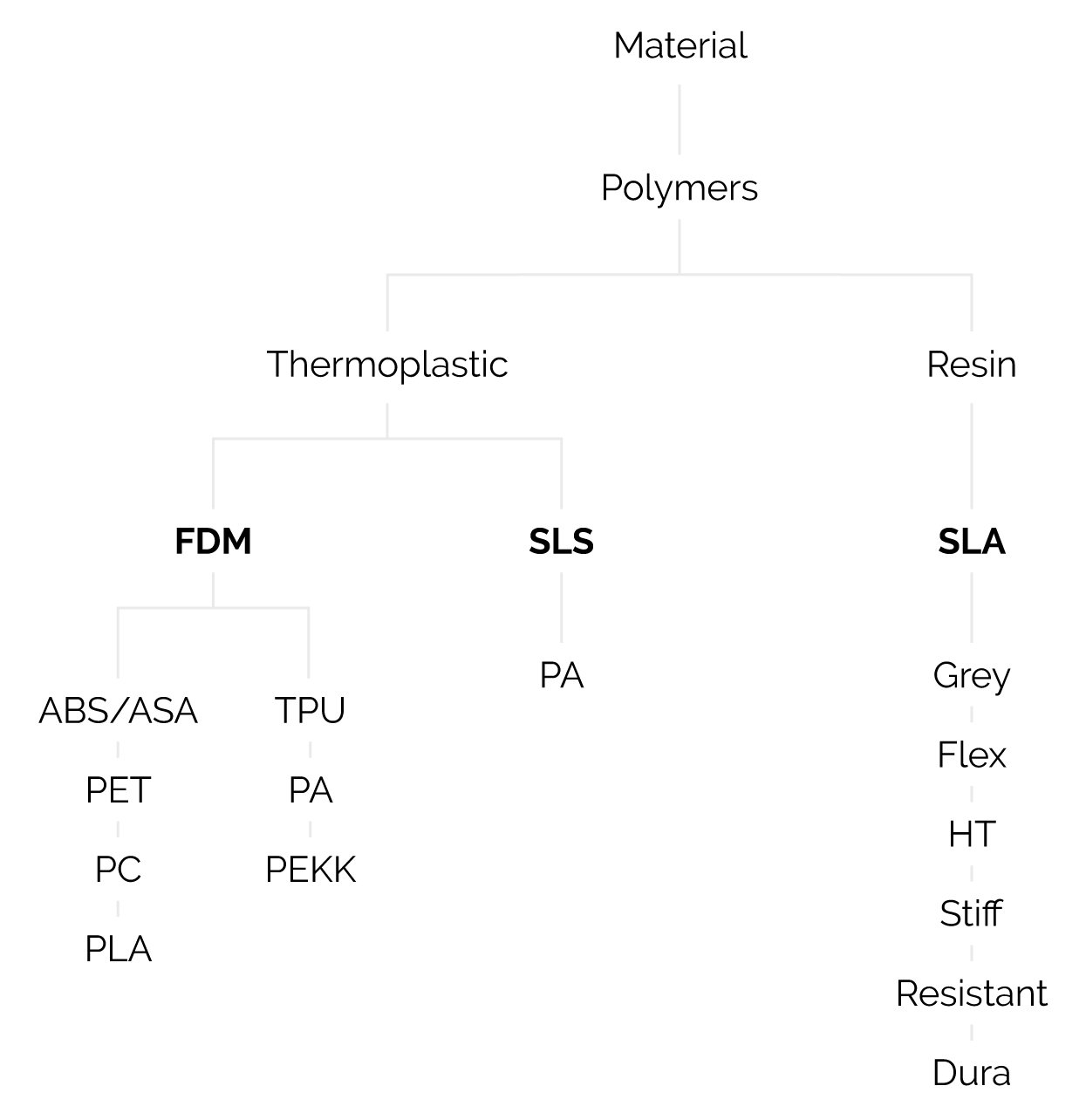
1. Selection of the Process Based on Material
Thechoiceofpolymeris crucial to ensuringthedesiredproperties. Both thermoplasticsandresinsneed to beconsidered. For thermoplasticparts, manufacturingiscarried out using FDM (FusedDepositionModeling) and SLS (Selective Laser Sintering) technologies.
The FDM (Fused Deposition Modeling) process offers an economical and versatile production of a wide variety of geometries, making it ideal for rapid prototyping and parts with moderate mechanical requirements.
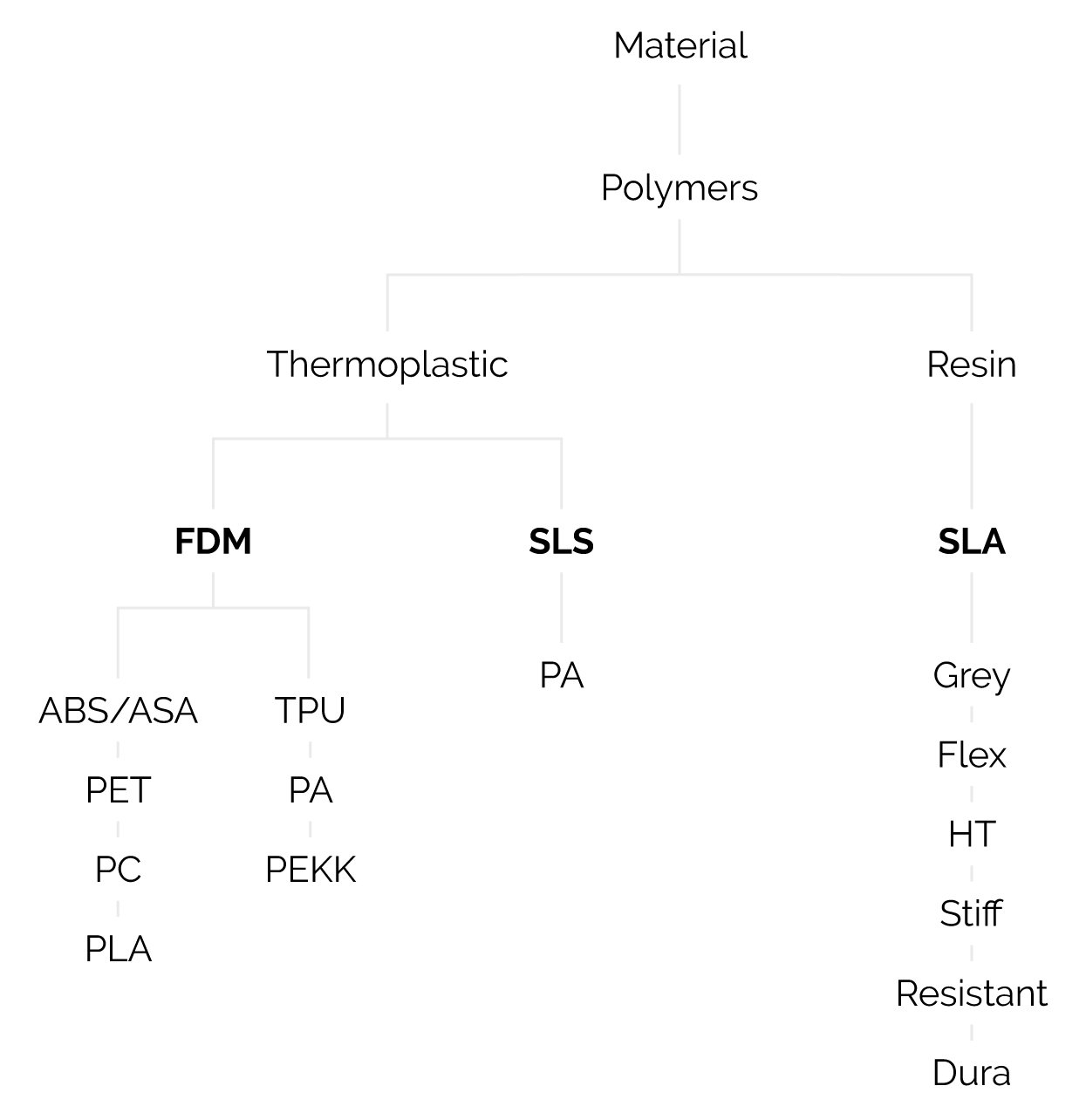
1. Selection of the Process Based on Material
Thechoiceofpolymeris crucial to ensuringthedesiredproperties. Both thermoplasticsandresinsneed to beconsidered. For thermoplasticparts, manufacturingiscarried out using FDM (FusedDepositionModeling) and SLS (Selective Laser Sintering) technologies.
The FDM (Fused Deposition Modeling) process offers an economical and versatile production of a wide variety of geometries, making it ideal for rapid prototyping and parts with moderate mechanical requirements.
SLS (Selective Laser Sintering) enables the production of parts suitable for high-performance industrial applications, with greater durability and a higher level of complexity, without the need for support structures.
For resin parts, SLA (Stereolithography) technology is used. This process allows the production of parts with extremely high precision and intricate details, making it ideal for applications that require smooth surfaces and complex geometries, such as in the jewellery industry, dentistry, and high-detail prototyping.
It should be noted that the material used to manufacture the part depends on the intended functional use. It may be practical or purely visual and aesthetic.
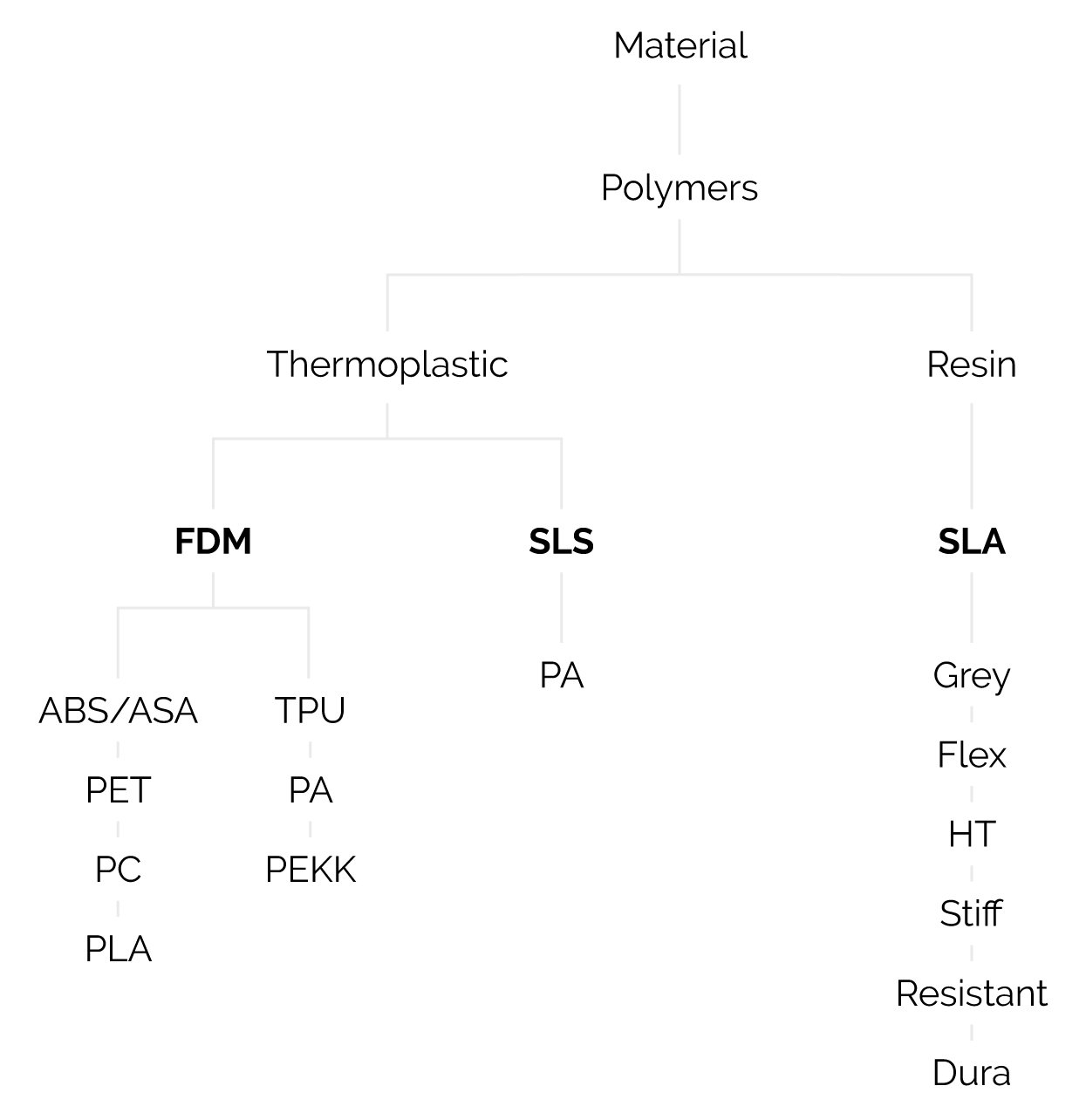
1. Selection of the Process Based on Material
Thechoiceofpolymeris crucial to ensuringthedesiredproperties. Both thermoplasticsandresinsneed to beconsidered. For thermoplasticparts, manufacturingiscarried out using FDM (FusedDepositionModeling) and SLS (Selective Laser Sintering) technologies.
The FDM (Fused Deposition Modeling) process offers an economical and versatile production of a wide variety of geometries, making it ideal for rapid prototyping and parts with moderate mechanical requirements.
SLS (Selective Laser Sintering) enables the production of parts suitable for high-performance industrial applications, with greater durability and a higher level of complexity, without the need for support structures.
For resin parts, SLA (Stereolithography) technology is used. This process allows the production of parts with extremely high precision and intricate details, making it ideal for applications that require smooth surfaces and complex geometries, such as in the jewellery industry, dentistry, and high-detail prototyping.
It should be noted that the material used to manufacture the part depends on the intended functional use. It may be practical or purely visual and aesthetic.
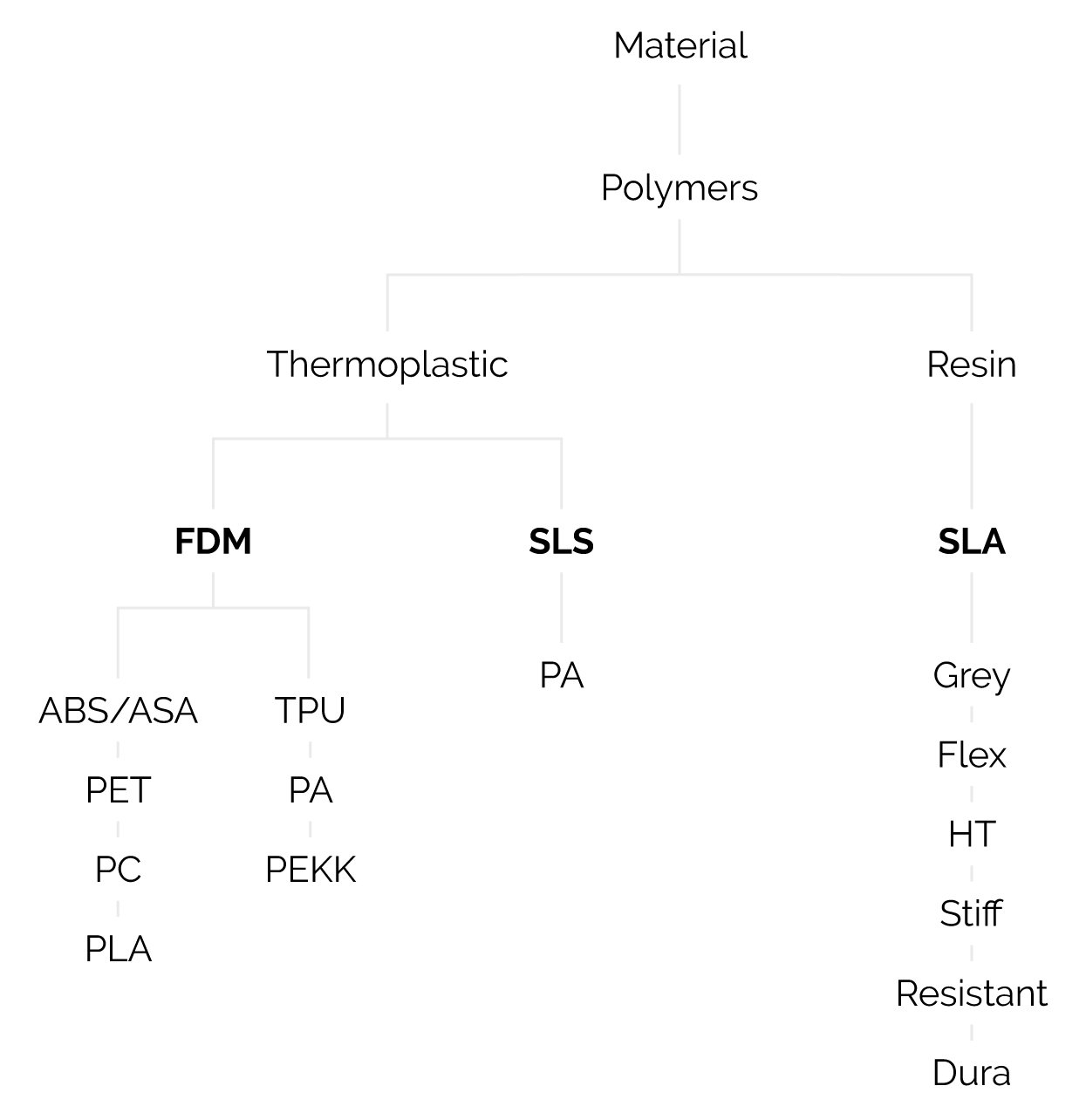
For resin parts, SLA (Stereolithography) technology is used. This process allows the production of parts with extremely high precision and intricate details, making it ideal for applications that require smooth surfaces and complex geometries, such as in the jewellery industry, dentistry, and high-detail prototyping.
It should be noted that the material used to manufacture the part depends on the intended functional use. It may be practical or purely visual and aesthetic.
SLS (Selective Laser Sintering) enables the production of parts suitable for high-performance industrial applications, with greater durability and a higher level of complexity, without the need for support structures.
For resin parts, SLA (Stereolithography) technology is used. This process allows the production of parts with extremely high precision and intricate details, making it ideal for applications that require smooth surfaces and complex geometries, such as in the jewellery industry, dentistry, and high-detail prototyping.
It should be noted that the material used to manufacture the part depends on the intended functional use. It may be practical or purely visual and aesthetic.
2. Selection of the Process According to Utilisation
The functionality of the part and its final use determine the most suitable technology. The analysis of functionality should begin by considering aspects such as form accuracy, geometry, and precision.
There are also other considerations for choosing the technology, such as whether the part will be used in environments with demanding conditions.
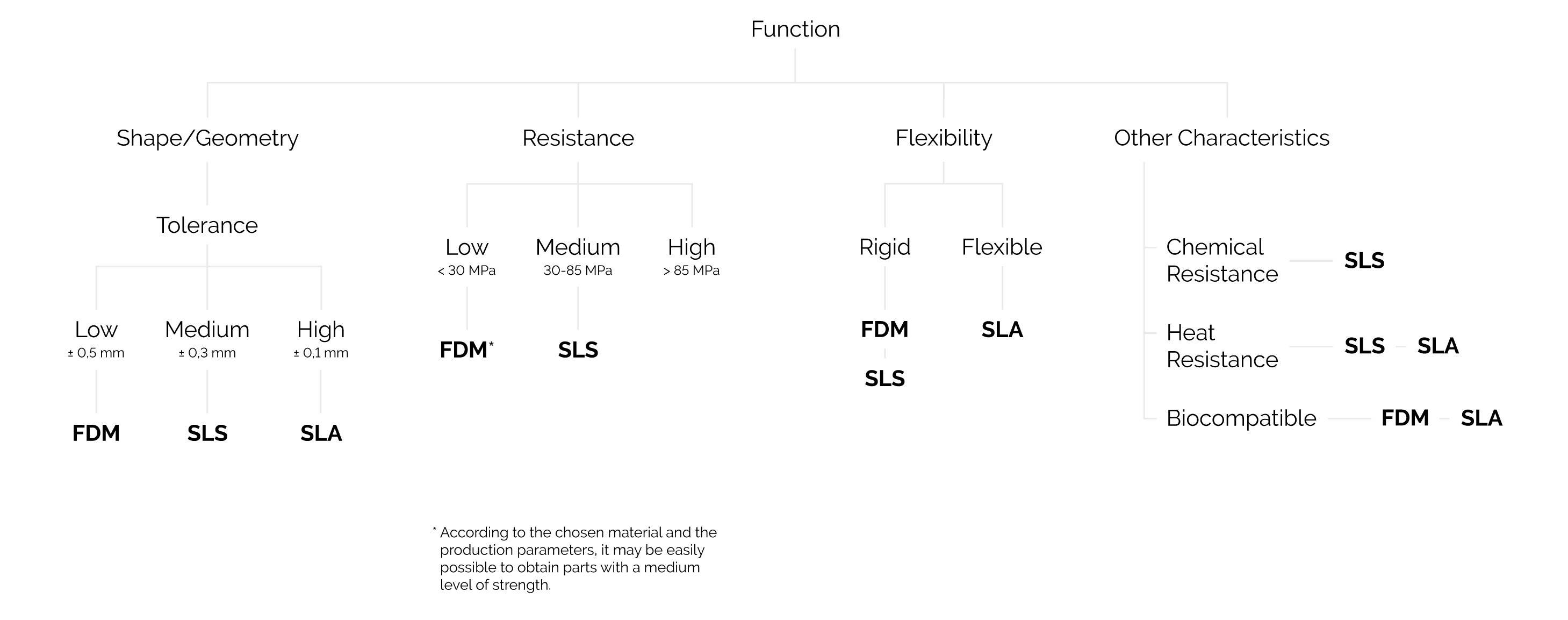
3. Selection of the Process with a Focus on Visual Appearance
Surface Quality:
- SLA (Stereolithography): Ideal for parts that require an extremely smooth surface with no visible layer marks, such as high-aesthetic products, presentation models, and precision moulds.
- FDM (Fused Deposition Modeling):Suitable for prototypes and functional parts where surface appearance is less critical. Layers may be visible, which might require post-processing if a smooth finish is needed.
- SLS (Selective Laser Sintering):Offers a slightly rough surface with a granular texture due to the use of powders. Ideal for functional parts or finishes that can tolerate a textured surface.
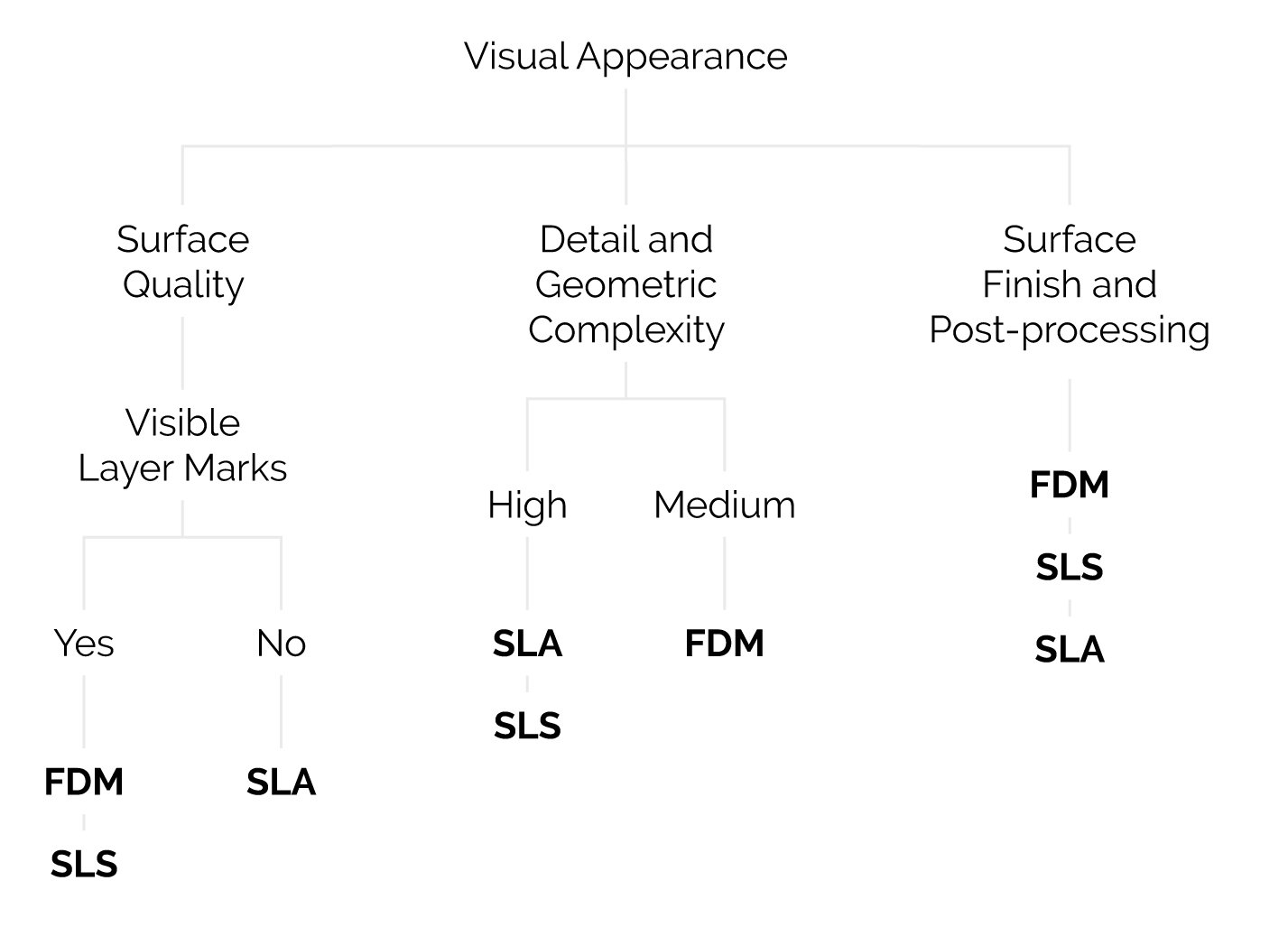
3. Selection of the Process with a Focus on Visual Appearance
Surface Quality:
- SLA (Stereolithography): Ideal for parts that require an extremely smooth surface with no visible layer marks, such as high-aesthetic products, presentation models, and precision moulds.
- FDM (Fused Deposition Modeling):Suitable for prototypes and functional parts where surface appearance is less critical. Layers may be visible, which might require post-processing if a smooth finish is needed.
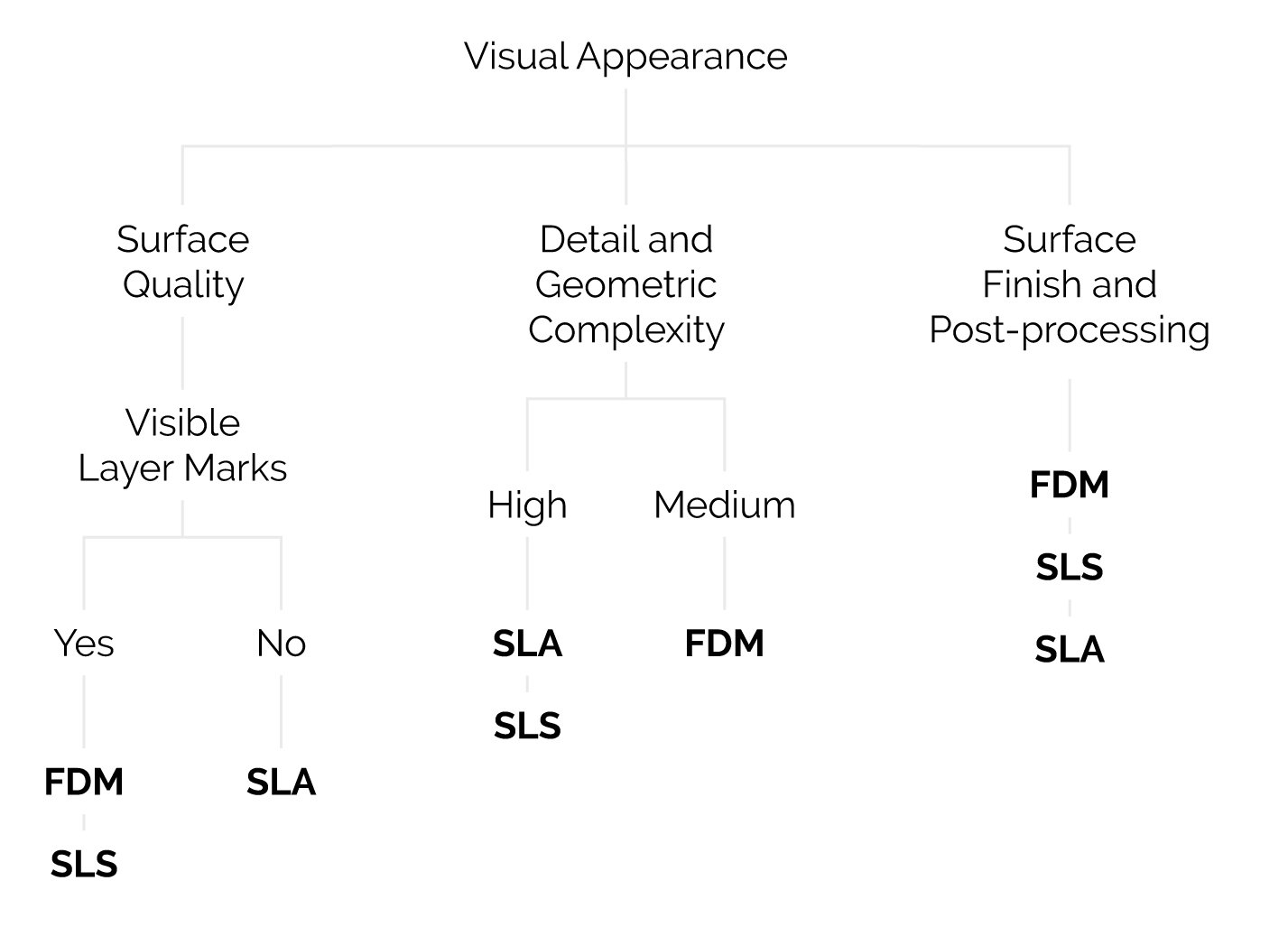
3. Selection of the Process with a Focus on Visual Appearance
Surface Quality:
- SLA (Stereolithography): Ideal for parts that require an extremely smooth surface with no visible layer marks, such as high-aesthetic products, presentation models, and precision moulds.
- FDM (Fused Deposition Modeling):Suitable for prototypes and functional parts where surface appearance is less critical. Layers may be visible, which might require post-processing if a smooth finish is needed.
-
- SLS (Selective Laser Sintering):Offers a slightly rough surface with a granular texture due to the use of powders. Ideal for functional parts or finishes that can tolerate a textured surface.
Detail Resolution and Geometric Complexity:
- SLA: Superior in reproducing fine details and creating complex geometries, with high resolution allowing the manufacture of tiny and intricate features.
-
- FDM: Better for parts with simple to moderately complex geometries, but with limitations in resolving small details, especially on curved or angled surfaces.
- SLS: Good for complex geometries, especially in functional parts where structural integrity is more important than fine finishing. Allows for the creation of parts with complex internal details, without the need for supports.
Surface Finishing and Post-processing:
- SLA: Produces parts that often require little or no post-processing to achieve a high-quality finish. However, if support structures are needed, they must be removed, which can significantly affect the supported surfaces.
- FDM: Parts generally require post-processing such as polishing or coating to improve appearance and reduce layer visibility. Supported surfaces significantly lose their surface quality.
- SLS: SLS parts can be post-processed to enhance surface finish, such as polishing, dyeing, or coating. However, the original granular texture may still be perceptible.
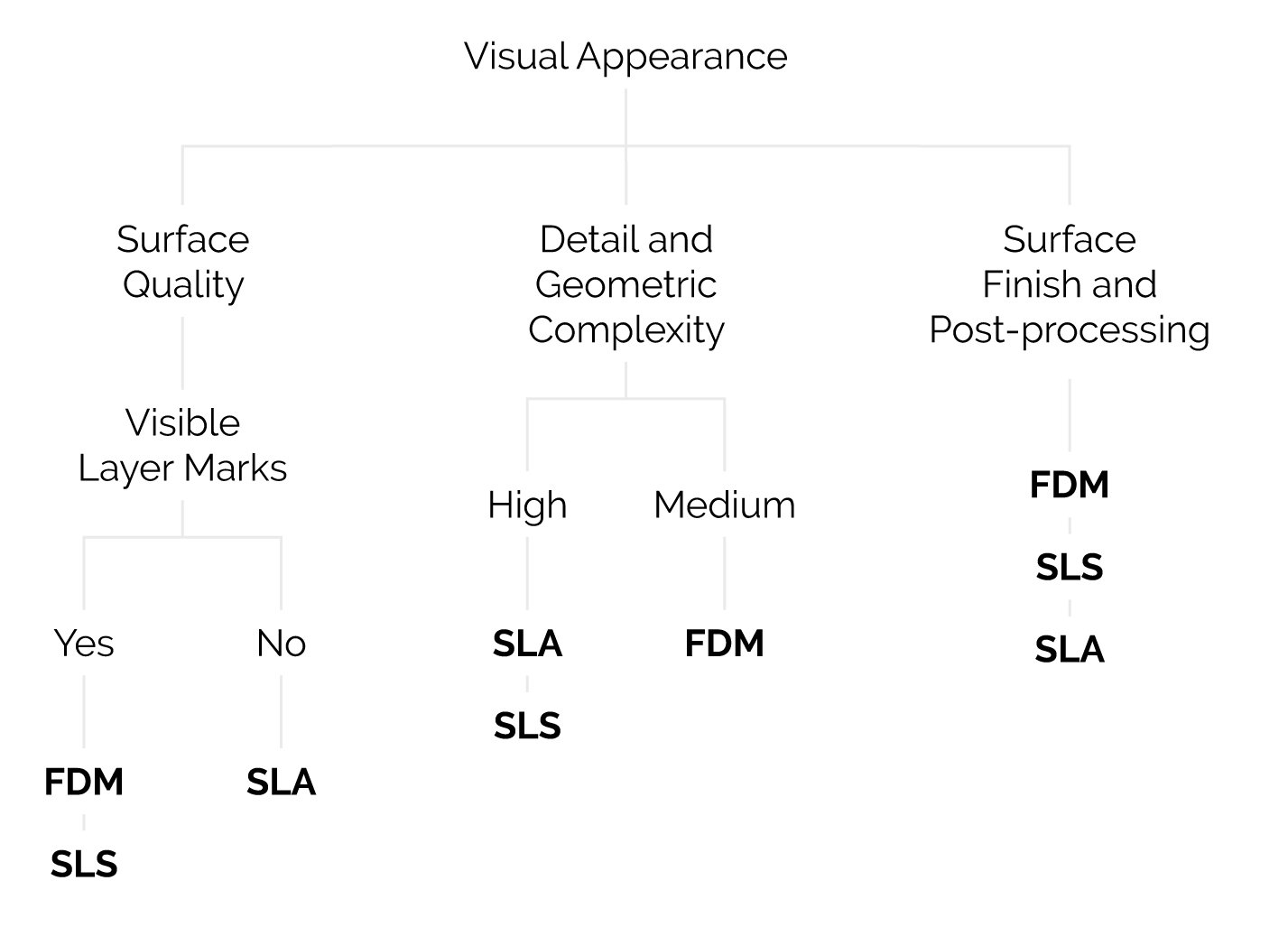
3. Selection of the Process with a Focus on Visual Appearance
Surface Quality:
- SLA (Stereolithography): Ideal for parts that require an extremely smooth surface with no visible layer marks, such as high-aesthetic products, presentation models, and precision moulds.
- FDM (Fused Deposition Modeling):Suitable for prototypes and functional parts where surface appearance is less critical. Layers may be visible, which might require post-processing if a smooth finish is needed.
- SLS (Selective Laser Sintering):Offers a slightly rough surface with a granular texture due to the use of powders. Ideal for functional parts or finishes that can tolerate a textured surface.
Detail Resolution and Geometric Complexity:
- SLA: Superior in reproducing fine details and creating complex geometries, with high resolution allowing the manufacture of tiny and intricate features.
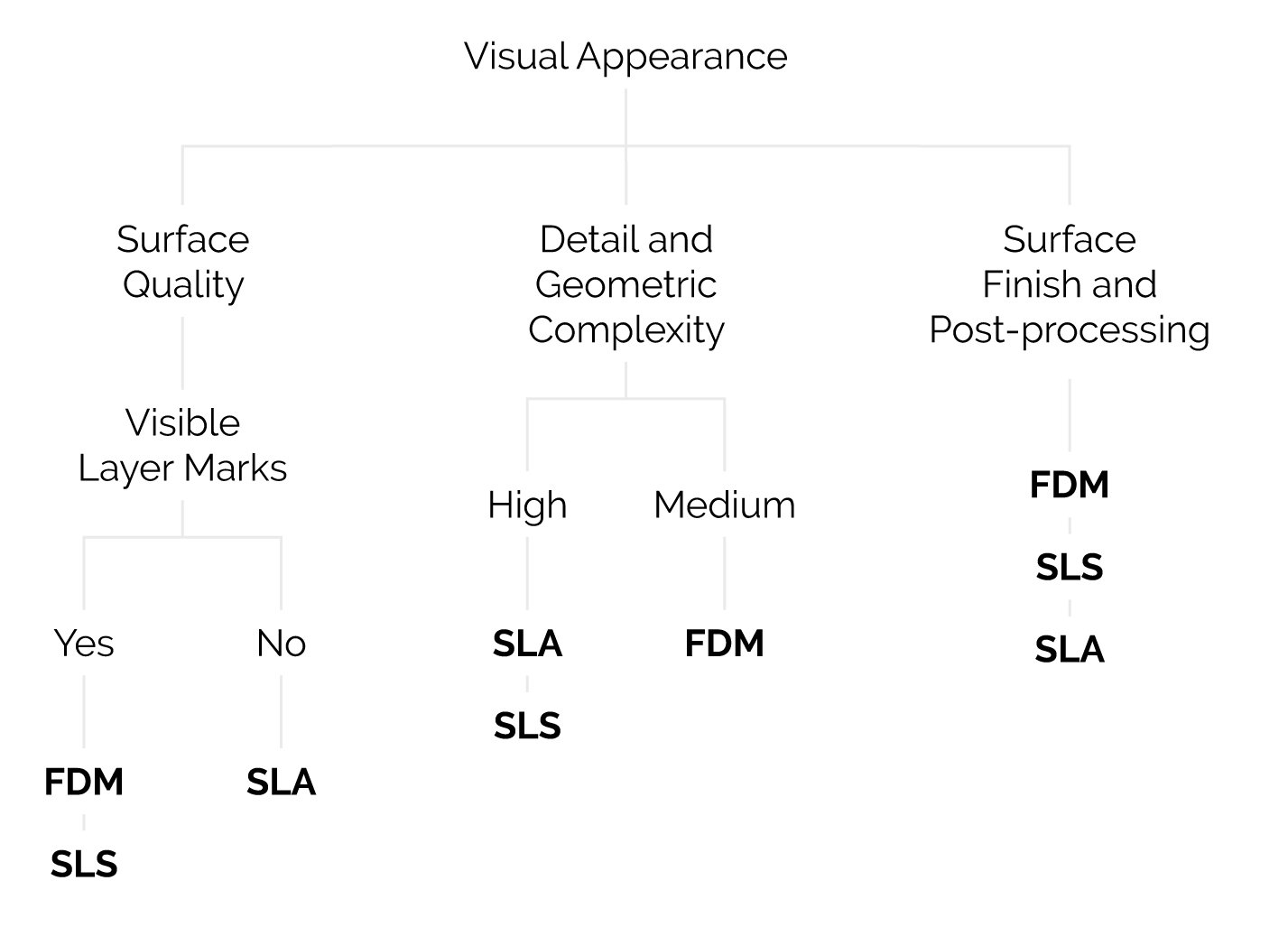
Detail Resolution and Geometric Complexity:
- SLA: Superior in reproducing fine details and creating complex geometries, with high resolution allowing the manufacture of tiny and intricate features.
-
- FDM: Better for parts with simple to moderately complex geometries, but with limitations in resolving small details, especially on curved or angled surfaces.
- SLS: Good for complex geometries, especially in functional parts where structural integrity is more important than fine finishing. Allows for the creation of parts with complex internal details, without the need for supports.
Surface Finishing and Post-processing:
- SLA: Produces parts that often require little or no post-processing to achieve a high-quality finish. However, if support structures are needed, they must be removed, which can significantly affect the supported surfaces.
- FDM: Parts generally require post-processing such as polishing or coating to improve appearance and reduce layer visibility. Supported surfaces significantly lose their surface quality.
- SLS: SLS parts can be post-processed to enhance surface finish, such as polishing, dyeing, or coating. However, the original granular texture may still be perceptible.
- SLS (Selective Laser Sintering):Offers a slightly rough surface with a granular texture due to the use of powders. Ideal for functional parts or finishes that can tolerate a textured surface.
Detail Resolution and Geometric Complexity:
- SLA: Superior in reproducing fine details and creating complex geometries, with high resolution allowing the manufacture of tiny and intricate features.
-
- FDM: Better for parts with simple to moderately complex geometries, but with limitations in resolving small details, especially on curved or angled surfaces.
- SLS: Good for complex geometries, especially in functional parts where structural integrity is more important than fine finishing. Allows for the creation of parts with complex internal details, without the need for supports.
Surface Finishing and Post-processing:
- SLA: Produces parts that often require little or no post-processing to achieve a high-quality finish. However, if support structures are needed, they must be removed, which can significantly affect the supported surfaces.
- FDM: Parts generally require post-processing such as polishing or coating to improve appearance and reduce layer visibility. Supported surfaces significantly lose their surface quality.
- SLS: SLS parts can be post-processed to enhance surface finish, such as polishing, dyeing, or coating. However, the original granular texture may still be perceptible.
- FDM: Better for parts with simple to moderately complex geometries, but with limitations in resolving small details, especially on curved or angled surfaces.
- SLS: Good for complex geometries, especially in functional parts where structural integrity is more important than fine finishing. Allows for the creation of parts with complex internal details, without the need for supports.
Surface Finishing and Post-processing:
- SLA: Produces parts that often require little or no post-processing to achieve a high-quality finish. However, if support structures are needed, they must be removed, which can significantly affect the supported surfaces.
- FDM: Parts generally require post-processing such as polishing or coating to improve appearance and reduce layer visibility. Supported surfaces significantly lose their surface quality.
- SLS: SLS parts can be post-processed to enhance surface finish, such as polishing, dyeing, or coating. However, the original granular texture may still be perceptible.
4. Selection of the Process Based on Production Capabilities
Production capacities must be taken into account when selecting an additive manufacturing process, and for this analysis there are a number of aspects that must be considered, such as dimensional accuracy, build volume, the need or not for support structures and, finally, the height of the layer.
Dimensional accuracy influences the level of detail and the quality of the print. The build volume defines the maximum dimensions of the piece. The need for support structures impacts design freedom. Processes that don't require support allow for the creation of complex structures. Layer height affects surface smoothness, where thinner layers result in smoother, more precise surfaces.
Alongside this guide and with the technical support from REIMAN and RMN Additive, the desired results can be more easily achieved by considering these factors and leveraging the expertise of our specialized team.
This article was referenced:
Silva, Francisco. 3D Printing: Technologies, Materials, and Applications.Quântica Editora, 2023.