We use cookies to make your experience better. To comply with the new e-Privacy directive, we need to ask for your consent to set the cookies. Learn more.
Solution for Pallet Stackers/Dispensers
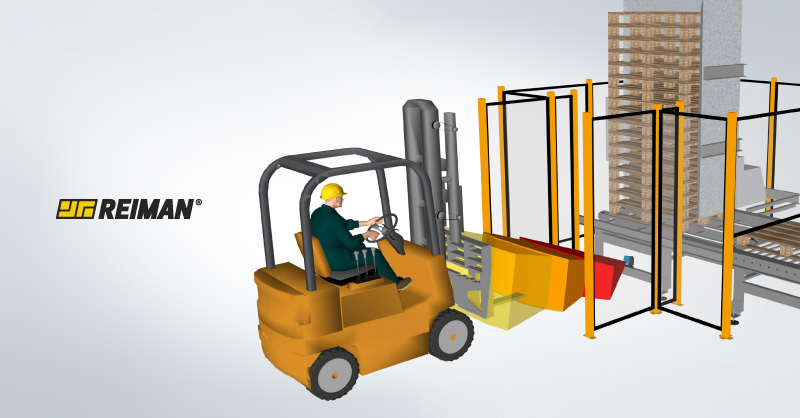
The harmonized standard EN 415-4 specifies safety requirements for packaging machines, including pallet stackers/dispensers. Its latest version goes further and clearly defines the safety interaction process between this specific type of equipment and peripherals, such as pallet stackers.
This fact will require some equipment manufacturers and integrators to go to packaging areas, making them susceptible to changes and improvements in the safety of their products.
This article aims to clarify the advantages of utilizing Inxpect products as a solution to ensure compliance with mandatory safety standards.
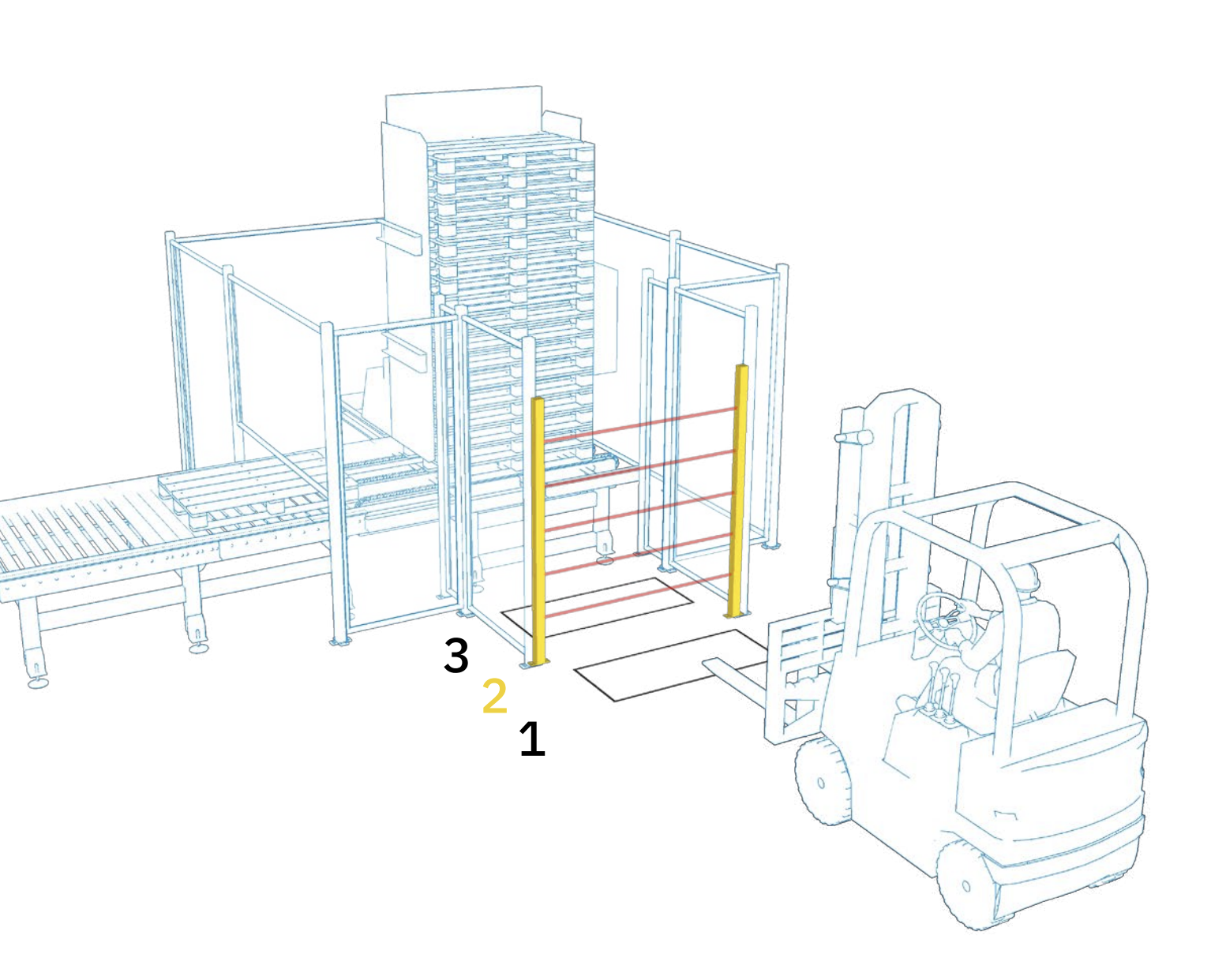
In the adjacent image, we can see an example of a more traditional safety solution, still without the use of Inxpect’s radar technology.
According to the mentioned standard, to stop the machine safely, the stacker must activate the first detection circuit (1), then the safety barrier (2), and finally the second detection circuit (3). The reverse sequence will automatically restart the machine (3→2→1).
When the stacker leaves the danger zone in the correct sequence, safety is not guaranteed if a second operator still remains inside it.
A new approach to machine safety involves the use of Inxpect’s radar technology, certified for industrial use. It is capable of detecting human presence volumetrically and without fail, thus preventing incidents or even accidents in industrial equipment.
This is only possible because when in Restart Prevention mode, Inxpect’s sensors can detect micro-movements, such as those of a human body, of an operator or a maintenance team member, when they are in a monitored danger zone.
Operating modes for Inxpect solutions, either exclusively or automatically combined:
Access Protection Mode
Ensures that the operator is always detected before reaching the danger zone.
Restart Prevention Mode
Ensures that when the operator is in the danger zone, the subject is always detected.
Therefore, the use of this new technology in industrial equipment represents a significant technological advancement and an incredible increase in the guarantee of people’s safety.
In addition to complying with the legal regulations by manufacturers and integrators of industrial equipment, this allows them to significantly increase the value of their solutions, with a competitive investment and high ROI.

In the adjacent image, we can see the same example presented earlier, but this time integrating Inxpect’s innovative radar-based solution.
An Inxpect sensor configured with three detection zones, paired with one Inxpect controller with safe industrial communication, is capable to detect a stacker and an operator in accordance with the EN 415-4, in the previously mentioned sequence.
Just one sensor to comply with the EN 415-4:2022 standard!
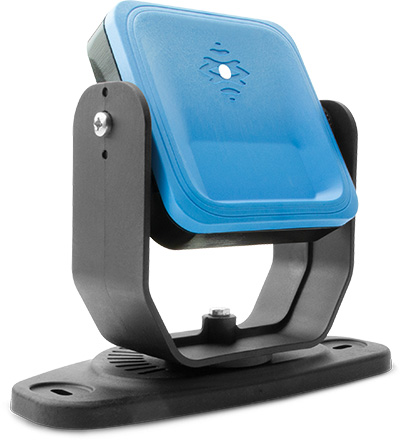
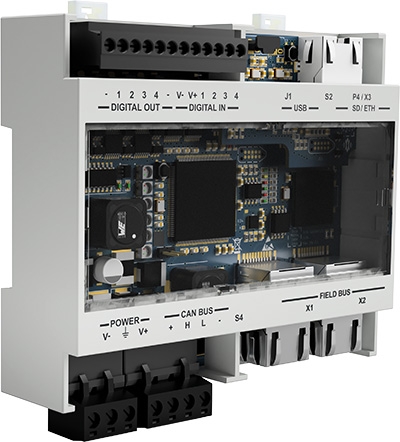

Unlike detection circuits and light barriers, Inxpect sensors ensures safety even when the stacker leaves the danger zone in the correct sequence and a second operator still remains in the area.
The sensors continue to detect their presence and the associated controller prevents the machine from being rearmed.
Inxpect’s radar technology works where optical sensors fail! Where they generate false alarms because they are influenced by the surrounding conditions, detecting dust, smoke, debris and spotlights. This drastically reduces equipment productivity and even contributes to increasing scrap volume.
Inxpect’s sensors are qualified to work in industrial environments, such as pallet handling, simplifying the interaction between operators and equipment, increasing their availability and
guaranteeing safety.
In summary, in addition to solving industrial security problems and guaranteeing increased equipment availability, Inxpect’s radar technology adds other benefits to this type of applications, such as:
- Reduction of installation and maintenance costs.
- Cost efficiency: one control unit can be linked up to six smart sensors, all operating independently.
- Performance level (PL) higher than the C level required by the standard.